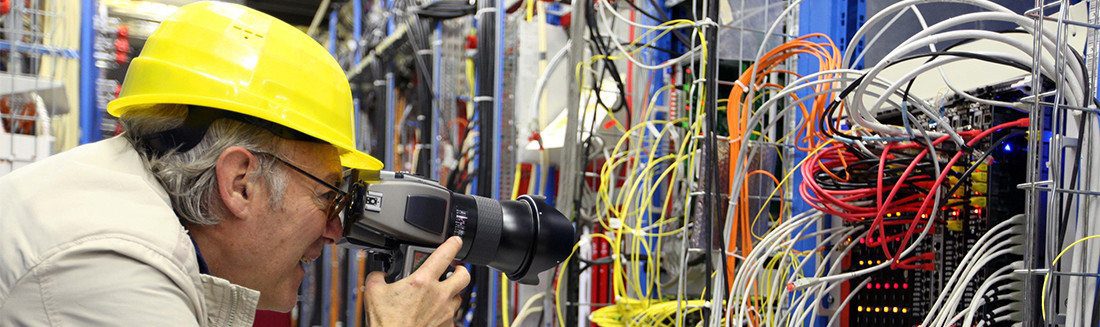
Four problems that make management systems static

Management systems are often documented in Word and Visio. This makes it cumbersome for making continuous minor adjustments. For this reason, they are only changed a few times a year. Does this mean that the company is no longer learning, or does it mean that many management systems have become too static? In this article, I will make a case for the latter.
The article is based on my personal conversations with more than 120 QA managers. I asked: “How frequently do you modify your management system?” to which the QA manager answers that it is done in connection with annual audits, management reviews, or when required by the CAPA process. This fulfils perfectly what is required according to the Quality Manual and the ISO 9001 standard. Still, the question is whether it’s enough?
Once we delve a little deeper into the conversation, it often turns out that four problems contribute to infrequent updating of management systems and process documentation:
Problem 1: Management systems take too long to update
Most management systems were written long ago. At a time when we used Word for text and Visio for diagrams. Later on, SharePoint was added, making it so just a few could find and correct the files. There is great control ensuring that no one makes unauthorized changes. This is important. But is it simple? Let’s look at the typical management system update process:
- A submission is reported and analyzed, resulting in a need for alteration.
- Interdisciplinary groups of employees meet in-person to identify and determine the change.
- A QA employee finds the original Word file and corrects text and revision history. Subsequent alterations may be required in Visio, where links need to be made to documents, images have to be copied into Word documents, etc.
- Now the change may go into a round of revisions with the relevant managers – often sequentially (meaning it may well take weeks).
- Step 3 is repeated.
- Finally, everything is saved as a PDF and sent to the relevant employee group by e-mail.
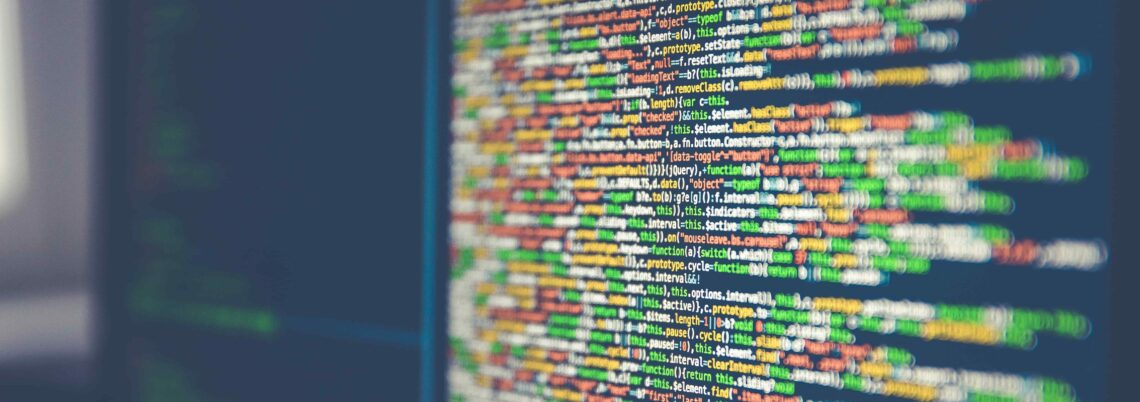
It goes without saying that before this process can be initiated, the change needs to be important. What, then, about the small daily requirements for the change? When the accountant and the technical manager realize that it is easier for the latter to send the purchase order and speak directly with the suppliers? This requires the movement of an activity from one role to the other. Is that the sort of thing you let pile up, forget about, or do you really initiate this time-consuming process? For practical purposes, the result will probably be the accountant and the technical manager making the change themselves in all actuality, and the management system not being updated.
We have previously done a few case studies with companies that use a combination of Word, SharePoint and Visio, but where hard-working and conscientious QA managers still keep the process documentation of the management system updated. Here’s an example (in Danish):
Problem 2: No deviations are reported by employees
I ask the question: How can your employees submit suggestions for improvements?
“You log into the system. Then you click down through the hierarchy to the proper procedure. Then, at the bottom, there’s a link. Here you can open a form and enter your suggestion. From here it will be addressed at an upcoming meeting.”
The answer illustrates that the next problem springs from the first. It’s all about everything being too heavy. We see a long discrepancy or complaint forms in many places. The process for CAPA or complaints assumes that the employee is totally on top of the ideal process, so he or she can spot the deviation when it takes place. At this point, you stop work and start looking for the form. Once it’s been found, you spend a half-hour to an hour documenting the discrepancy, after which it is submitted. Let’s be brutally honest: Who thinks busy employees do this?
And I haven’t even begun to talk about the problem of employees themselves making mistakes that they now need to spend time bringing to the attention of their supervisors.
Problem 3: The management system is too general
Many places have management systems with very general descriptions. The more general the information, the more rarely it needs updating. Smart when it comes to spending the least possible amount of time on this, but maybe not so smart when it comes to the relevance of the management system.
The QA manager is caught in something of a dilemma. On one hand, it’s a fact that when processes and procedures are described very generally, they match up with the work and the perceptions of the rest of the organization.
“Here is our process hierarchy. It’s divided according to our main processes: Sales & Marketing, Purchasing, Production, and Logistics. Our Sales and Marketing Manager owns the process for sales and marketing.”
Hard to get an argument here. On the other hand, what does it contribute as far as the rest of the organization is concerned? Not exactly process orientation. On the other hand, it’s almost impossible to go into detail when management systems are so difficult to update, and not least to communicate.
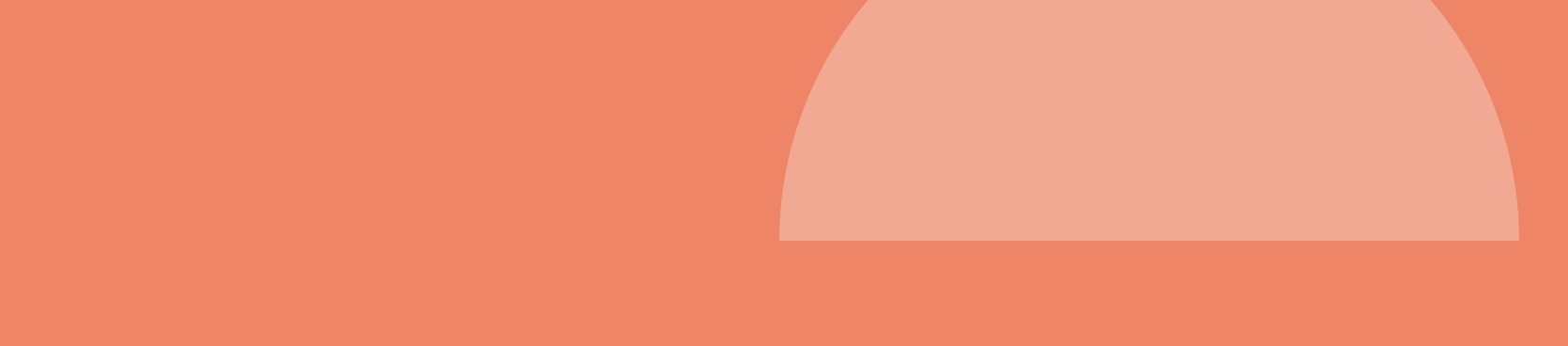
Try Gluu for free
Sign up for a 30-day trial.
No credit card required.
Problem 4: Improvements and the management system are two different things
In several companies, the QA department is centrally located, while improvements often take place at stand-ups on the factory floor. This is where learning takes place and this is where the actual processes are implemented. Unfortunately, they are not interdisciplinary. In this way, the interdisciplinary improvements are rarely implemented. Nobody works against the heavy management system.
How is a management system made more dynamic and relevant?
On this basis, it’s no wonder that the rest of the organization often experiences the management system as a sort of graveyard for documentation for the auditors that drop by from time to time. The question is how management systems can be made more dynamic? In my opinion, it comes down to two things: Simplicity and involvement.
“It’s about simplicity and involvement”
First, it needs to be much easier to come up with ideas and deviations and analyze these and implement the changes. Imagine if the management system was a webshop. How many actions does it take before the change is implemented? The more, the fewer changes, and the more static the management system becomes. The more static, the more irrelevant.
Next, the changes have to be implemented in as decentralized way as possible. If the marketing coordinator handles the production of sales materials, then why not let her own and update the process? In the same way, process owners need to have real ownership and be responsible for the updates and the process documentation tool. The Quality Manager needs to facilitate the work, ensure that the tools are okay, and otherwise just be the “backstop with veto power” when frequent changes risk running afoul of external requirements.
So, brutally honest now – How often do you adjust your management system? Is it easy to do? Do you get a lot of input from your employees?
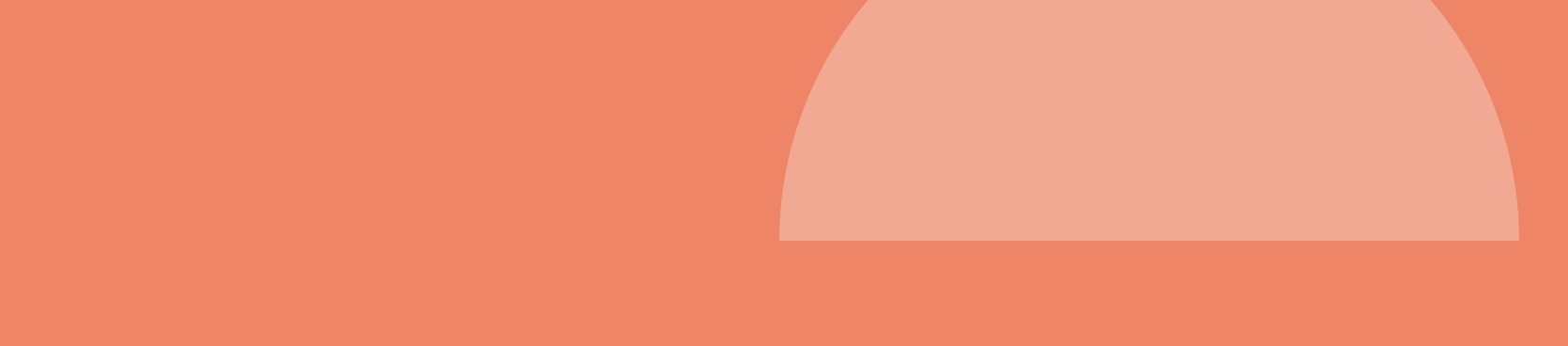
Try Gluu for free
Sign up for a 30-day trial.
No credit card required.
Frequently Asked Questions
To keep process documentation current and dynamic, regular reviews and updates are necessary. Utilizing a digital document control system can ensure everyone uses the latest version. Creating a centralized repository for all documents ensures consistency. Encouraging employee feedback can add practical insights to the documentation.
However, keeping documentation dynamic has its challenges. It can be time-consuming, especially in larger organizations with numerous complex processes. Ensuring consistency across all documents can be difficult when many employees handle different documents. Resistance from employees unopen to changes can also be a challenge.
The frequency of reviewing the documentation depends on factors such as business dynamics, internal changes, and industry regulations. Generally, an annual review is recommended but immediate updates should be made when significant process changes occur. Cultivating a continuous improvement culture helps keep the documentation relevant and dynamic.