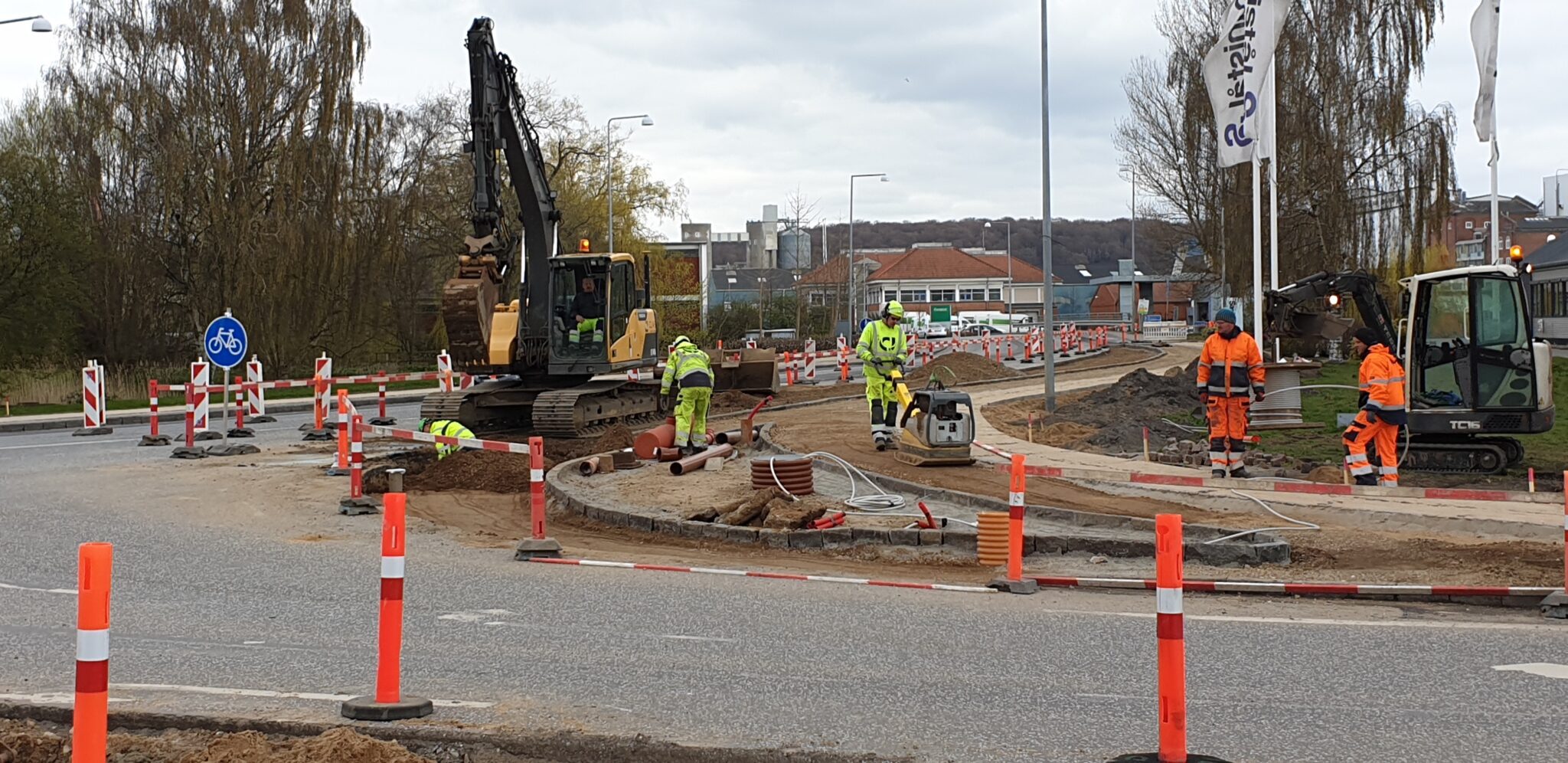
CASE STUDY
Scaling Up with Confidence: How Gluu’s Processes Ensure Quality and Customer Focus
Growth is one thing. Ensuring that it doesn’t hurt quality and customer focus required a new construction process management approach and tool at Danish contractor CJ A/S.
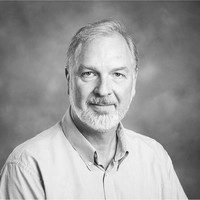
“Today we can follow all our projects from offer to delivery – all processes, activities and documents have been standardized so that all employees work in a standard way. ” Read case
Hans Jørgen Ebbesen,
CEO, CJ A/S
About Contractor CJ A/S
CJ A/S, founded in 2011, has grown into a strong and innovative construction company with expertise in Residential and Commercial, Industrial Services, Fuel Facilities, and Civil Engineering. With a team of over 160 professionals, they’ve completed nearly 400 projects of various scales. Their success is rooted in strong values and collaborative relationships, both within the team and with external partners. CJ is owned by key employees and guided by an experienced board. Their unwavering commitment to responsibility, integrity, and innovation has consistently led to impressive results and client satisfaction.
Situation — CJ was looking for a way to ensure that everyone worked in accordance with a common and updated ‘best practice‘ in all departments. This should include an approach to continuously optimize end-to-end processes with the customer in focus.
Problem — Running large construction projects well is hard. Planning, coordination and understanding of a customer’s needs is key in avoiding that the many interactions between the many different roles involved in a construction project lead to costly errors.
A key problem is that budget overruns usually fall back on construction companies – or they lead to costly and time-consuming arbitration.
All of these problems were already occuring at CJ even before the company started growing rapidly. CJ then experienced a surge in demand and this growth risked amplifying the problems when mew employees introduced their own ways of working based on their previous experiences into the mix.
Top management feared a dilution of the ‘CJ way of working’, which had created the initial success.
Solution — Gluu’s construction consultancy partner Refine Consulting lead the project. It started with getting top management fully aligned and committed around a single, standardized approach to work.
The ambition was set to map and digitalize all core end-to-end processes through the normal construction project phases of Offer, Design, Planning and Execution.
Gluu was selected as the collaborative process management tool that would underpin the effort right from the first mapping through to task execution on construction sites.
Implementation – Refine Consulting started by running a number of workshops at CJ. The goal was to identify the critical processes and shine a light on any shortcomings in the existing ways of working.
All processes, work instructions and documentation were reviewed and validated by selected employees. Continuous improvement events gave everyone involved the opportunity to bring their own experience to the table – to ensure that CJs best practice didn’t leave out important insights.
Based on this agile approach, they have been refined to the level that is used in production today.
Results — Since implementing Gluu in 2019 CJ has more than doubled in size. CJ now has…
- Full control over all construction management processes.
- Continuous process improvement through employee feedback.
- Effective construction process management that ensures a focus on customer needs -without budget overruns.
- Proper case management ensures that all employees are aware of where in the construction management process they are and what is expected by the customer.
CJs CEO expresses it this way:
“In Gluu, we can – throughout the process – see whether activities have been done and where we work is not moving. We can also see who is responsible for the specific activities. This way we can help each other to get things done in the right order and in a timely manner.”
Hans Jørgen Ebbesen, CEO, CJ A/S
More than 100 new employees have experienced a common starting point with standard processes and a common project portfolio overview.
Before Gluu there was a risk that every new employee would be working their own way. Now, Hans Jørgen explains that…
” The improvement ideas that constantly flow from our employees are all reported digitally, picked up by process owners, and some incorporated into our management system.”
With digital workflows in Gluu, new employee’s experiences can be embedded into existing processes, ensuring that CJ always works to the industry best practice.
The future – The experience from its construction sites means that CJ now is planning to include sales work, health and safety, equipment management and other areas in Gluu. The plan is to get Gluu into all corners of CJ’s production.
THE METHOD
Getting everyone onboard from standard processes to execution
Gluu is designed around a proven method for getting to a truly ‘process-driven’ company. In CJs case the effort was led by Refine Consulting and started with mapping ‘standard processes’ that represented the company’s best practice. These then became ‘shared processes’ as they invited employee feedback and improvement. Finally, tasks were added and processes are not executed with Gluu to drive real, tangible results in terms of lower risk and higher productivity.
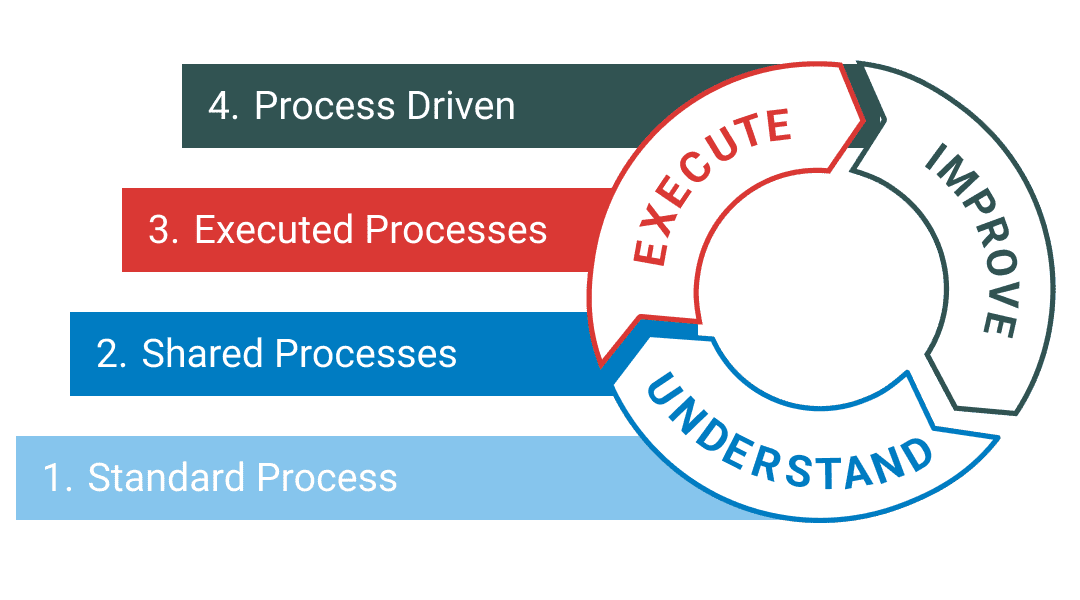
Lessons learned for others to use
CJ has only been able to apply the new production management process to new projects, since existing projects already were subject to existing contract and management.
So far, the bidding process has undergone more improvement cycles than the execution process has. Thus, the full picture of the improvements in production will only be clear at a later stage.
The value has been highest in large projects where tasks change hands several times. This is where they used to see most errors and delays.
The benefits for the large projects are clear in more areas:
- From a customer perspective, CJ can now guide the customer into a collaborative project mindset from day one. One reason is that the customer’s activities – and expectations – become very clear. All customer touchpoints are clear. CJ can say exactly what is going to happen and what actions, as well as tools, that will support the daily work between them and the customers.
- There is an optimization potential just in getting an overview of the process. The overview helps to avoid unnecessary shifts between employees internally, which must at the same time be able to replace each other on projects when circumstances require it.
- Construction process management and execution of tasks via Gluu provide another optimization potential: no one loses track, and all relevant and critical documentation follows the whole process. Anyone can, in the course of the project, tell the customer exactly what the status is and what is going to happen going forward.
In the smaller projects, it has primarily been a better overview and more efficient construction management, simpler IT and easier documentation that has provided value to projects. Finally, in close interaction with Bülow Management, a basic improvement culture is developed. Here, all the company’s employees contribute to improvement proposals directly in Gluu, which will help improve the company’s processes going forward.