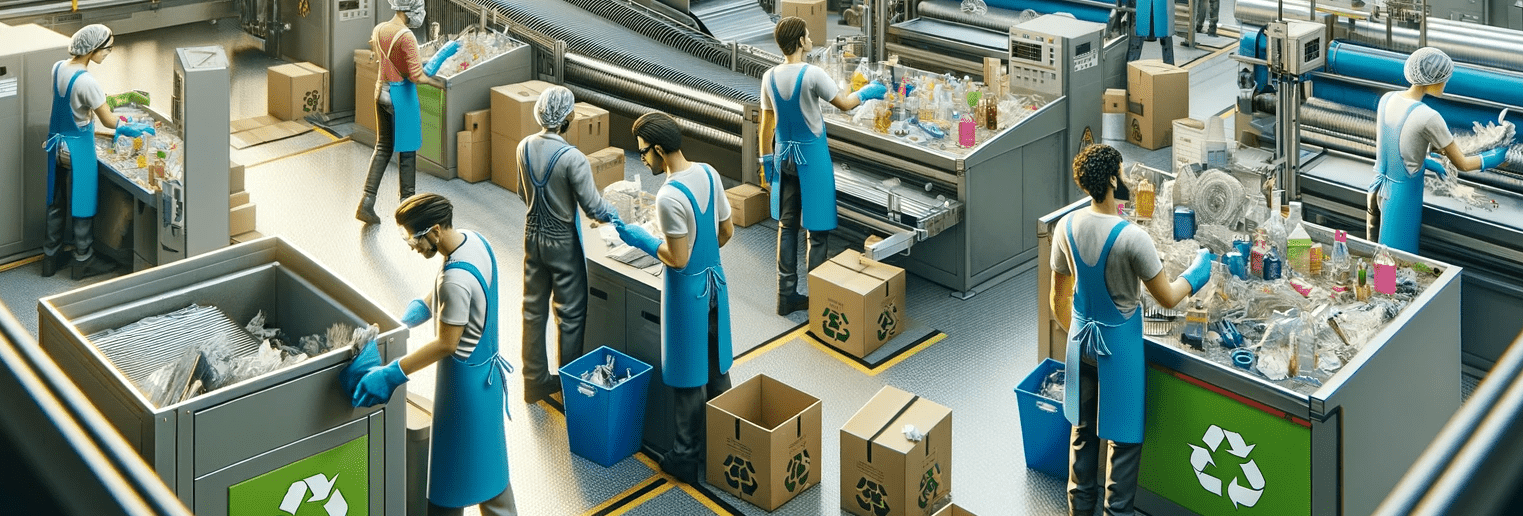
Lean process improvement: Removing the waste

Lean process improvement is a methodology that strives to eliminate waste and optimize productivity. By implementing lean principles, organizations can streamline their operations, improve efficiency, and deliver better value to their customers. In this article, we will explore what lean process improvement is, its benefits, and how it can be applied to reduce waste. We will also delve into the use of value stream mapping and the impact of standardization on waste reduction. Lastly, we will discuss the application of Kaizen techniques to further enhance process efficiency.
Table of contents
Looking for something else? Explore these related articles:
What Is Lean Process Improvement?
Lean process improvement, often referred to as lean manufacturing or lean management, is a systematic approach to identifying and eliminating waste in any form. Originally developed by Toyota in the 1940s, it has since been widely adopted by organizations across various industries. The core concept of lean process improvement is to create more value for customers with fewer resources.
Lean process improvement is based on several key principles, including:
Value: | Understanding what the customer considers valuable and focusing efforts on delivering that value. |
Value Stream: | Mapping out the entire process and identifying areas of waste and inefficiency. |
Flow: | Ensuring smooth and uninterrupted flow of work by removing bottlenecks and reducing lead times. |
Pull: | Producing based on customer demand rather than pushing products through the system. |
Perfection: | Ensuring the smooth and uninterrupted flow of work by removing bottlenecks and reducing lead times. |
When implementing lean process improvement, organizations often start by conducting a thorough analysis of their current processes. This involves mapping out the entire value stream, from the moment a customer places an order to the delivery of the final product or service. By visualizing the entire process, organizations can identify areas of waste, such as unnecessary waiting times, excessive inventory, or redundant steps.
Once the areas of waste are identified, organizations can then focus on eliminating them. This can be done through various techniques, such as standardizing work processes, implementing visual management systems, or using tools like Kanban boards to track progress. By continuously monitoring and improving the process, organizations can achieve higher levels of efficiency and effectiveness.
One of the key benefits of lean process improvement is its ability to enhance customer satisfaction. By understanding what the customer truly values and eliminating activities that do not add value, organizations can deliver products and services that better meet customer needs. This can result in increased customer loyalty, repeat business, and positive word-of-mouth referrals.
Furthermore, lean process improvement can also lead to significant cost savings. By eliminating waste and improving efficiency, organizations can reduce their operating costs, improve their profit margins, and gain a competitive advantage in the market. This can be particularly beneficial in industries with tight profit margins or high levels of competition.
Another advantage of lean process improvement is its focus on employee engagement and empowerment. By involving employees in the improvement process and giving them the tools and authority to make changes, organizations can tap into their knowledge and creativity. This not only leads to better solutions and ideas but also boosts employee morale and satisfaction.
In conclusion, lean process improvement is a powerful methodology that enables organizations to identify and eliminate waste, improve efficiency, and deliver greater value to customers. By embracing the principles of lean, organizations can achieve higher levels of customer satisfaction, cost savings, and employee engagement. Whether in manufacturing, healthcare, or service industries, lean process improvement has proven to be a valuable tool for organizations striving for continuous improvement and excellence.
Examples of Gluu features for Process Improvement
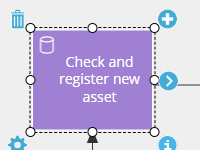
Simple process mapping
Map with five basic shapes to simplify understanding and use by employees across all levels.
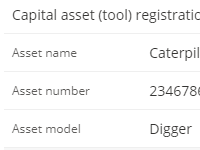
Embedded digital forms
Attach forms to tasks and capture responses via the mobile app exactly when work is being done.
Benefits of Lean Process Improvement
The implementation of lean process improvement can yield numerous benefits for organizations. Some of the key advantages include:
- Improved efficiency: By eliminating waste and optimizing processes, organizations can increase productivity and reduce unnecessary steps.
- When organizations embrace lean process improvement, they embark on a journey toward enhanced efficiency. By closely examining their workflows and identifying areas of waste, they can streamline their processes to eliminate any unnecessary steps. This optimization not only saves time but also ensures that resources are utilized effectively, resulting in improved overall efficiency.
- When organizations embrace lean process improvement, they embark on a journey toward enhanced efficiency. By closely examining their workflows and identifying areas of waste, they can streamline their processes to eliminate any unnecessary steps. This optimization not only saves time but also ensures that resources are utilized effectively, resulting in improved overall efficiency.
- Reduced costs: Lean process improvement helps minimize unnecessary expenses, such as excess inventory, overproduction, and rework.
- One of the primary goals of lean process improvement is to eliminate any activities that do not add value to the organization or the customer. By doing so, organizations can significantly reduce costs associated with excess inventory, overproduction, and rework. With lean principles in place, organizations can achieve cost savings while maintaining the same level of productivity, if not higher.
- One of the primary goals of lean process improvement is to eliminate any activities that do not add value to the organization or the customer. By doing so, organizations can significantly reduce costs associated with excess inventory, overproduction, and rework. With lean principles in place, organizations can achieve cost savings while maintaining the same level of productivity, if not higher.
- Enhanced quality: By focusing on value and reducing defects, organizations can deliver higher-quality products and services to their customers.
- Quality is a crucial aspect of any organization’s success. Lean process improvement emphasizes the importance of delivering value to customers by reducing defects and errors. By implementing robust quality control measures and continuously monitoring and improving processes, organizations can ensure that their products and services meet or exceed customer expectations. This commitment to quality not only enhances customer satisfaction but also strengthens the organization’s reputation in the market.
- Quality is a crucial aspect of any organization’s success. Lean process improvement emphasizes the importance of delivering value to customers by reducing defects and errors. By implementing robust quality control measures and continuously monitoring and improving processes, organizations can ensure that their products and services meet or exceed customer expectations. This commitment to quality not only enhances customer satisfaction but also strengthens the organization’s reputation in the market.
- Increased customer satisfaction: Lean process improvement aims to provide greater value to customers, resulting in improved satisfaction and loyalty.
- Customer satisfaction is at the heart of lean process improvement. By focusing on delivering value and continuously improving processes, organizations can meet and exceed customer expectations. When customers receive products and services that align with their needs and preferences, they are more likely to be satisfied and loyal to the organization. This increased customer satisfaction not only leads to repeat business but also generates positive word-of-mouth, attracting new customers.
- Customer satisfaction is at the heart of lean process improvement. By focusing on delivering value and continuously improving processes, organizations can meet and exceed customer expectations. When customers receive products and services that align with their needs and preferences, they are more likely to be satisfied and loyal to the organization. This increased customer satisfaction not only leads to repeat business but also generates positive word-of-mouth, attracting new customers.
- Empowered employees: The involvement of employees in lean process improvement initiatives promotes a culture of continuous improvement and gives them a sense of ownership.
- Engaging employees in lean process improvement initiatives is a fundamental aspect of its success. When employees are involved in identifying and implementing process improvements, they feel a sense of ownership and empowerment. This involvement fosters a culture of continuous improvement, where employees actively contribute their ideas and expertise to enhance organizational processes. Empowered employees are more motivated, productive, and committed to the organization’s success.
👉 Recommendation: Embrace lean process improvement to enhance efficiency, reduce costs, improve quality, increase customer satisfaction, and empower your employees. Start by identifying and eliminating waste in your workflows to optimize operations and deliver greater value to your customers.
Utilizing Value Stream Mapping for Waste Reduction
Value stream mapping is a powerful tool used in lean process improvement to identify and visualize the flow of materials and information required to deliver a product or service. By representing the entire value stream, from the customer’s request to the product’s completion, organizations can identify areas of waste and inefficiency.
When conducting value stream mapping, organizations consider both the physical and informational aspects of their processes. By analyzing the flow of materials, information, and work activities, they can identify bottlenecks, delays, and unnecessary steps. Moreover, this enables them to take targeted actions to reduce waste and streamline the value stream, ultimately improving overall process efficiency.
One of the key benefits of value stream mapping is its ability to provide a visual representation of the entire value stream. This allows organizations to easily identify and understand the various steps involved in delivering a product or service. By visually mapping out the value stream, organizations can gain a holistic view of their processes and identify areas for improvement.
Value stream mapping also helps organizations identify waste in their processes. Waste can take many forms, such as excess inventory, unnecessary transportation, or overproduction. By analyzing the value stream, organizations can pinpoint these areas of waste and take steps to eliminate or reduce them. It’s worth keeping in mind that this does not only improves efficiency but also reduces costs and improves customer satisfaction.
Another advantage of value stream mapping is its ability to facilitate collaboration and communication within an organization. By involving employees from different departments or functions in the mapping process, organizations can gain valuable insights and perspectives. This cross-functional collaboration can lead to innovative solutions and a shared understanding of the value stream, fostering a culture of continuous improvement.
”Time waste differs from material waste in that there can be no salvage. The easiest of all wastes and the hardest to correct is the waste of time, because wasted time does not litter the floor like wasted material.”
Henry Ford
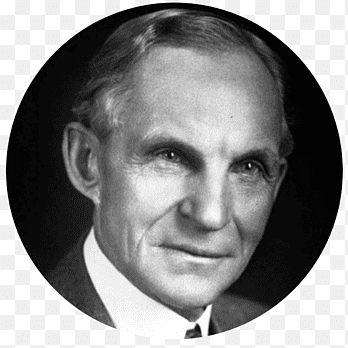
Furthermore, value stream mapping provides a baseline for measuring improvement. By documenting the current state of the value stream, organizations can track their progress over time. This allows them to evaluate the effectiveness of their improvement efforts and make data-driven decisions. By regularly updating the value stream map, organizations can ensure that their processes continue to evolve and improve.
In conclusion, value stream mapping is a valuable tool for organizations looking to reduce waste and improve process efficiency. By visually mapping out the entire value stream and analyzing it for waste, organizations can identify areas for improvement and take targeted actions. This not only improves efficiency but also reduces costs and enhances customer satisfaction. Additionally, value stream mapping facilitates collaboration and communication within an organization, leading to innovative solutions and a culture of continuous improvement.
Examining the Impact of Standardization on Waste
Standardization plays a crucial role in lean process improvement as it helps establish consistent processes and procedures. By implementing standardized work instructions, organizations can reduce variation and improve predictability, leading to waste reduction.
Standardization ensures that work is performed in a consistent manner, eliminating unnecessary variations and errors. It helps employees understand expectations and enables them to identify deviations from the standard. By continually improving and refining standardized processes, organizations can minimize waste caused by rework, defects, and inefficient practices.
Applying Kaizen Techniques to Streamline Processes
Kaizen, a Japanese term meaning “continuous improvement,” is a key component of lean process improvement. It involves making small, incremental changes to processes and systems to boost productivity and eliminate waste.
Kaizen techniques focus on empowering employees to identify and implement improvements in their daily work. This often involves brainstorming sessions, root cause analysis, and collaboration among team members. By leveraging the collective knowledge and experience of employees, organizations can drive continuous improvement and achieve sustainable results.
Some common Kaizen techniques include 5S, which focuses on workplace organization and cleanliness, and Kanban, a visual scheduling system that helps optimize inventory levels and production flow. By applying these techniques and encouraging a culture of continuous improvement, organizations can further streamline their processes and eliminate waste.
Conclusion
Lean process improvement is a powerful methodology for removing waste and optimizing productivity. By implementing lean principles, organizations can streamline their operations, improve efficiency, and deliver better value to their customers. Through the use of value stream mapping, standardization, and Kaizen techniques, organizations can identify and eliminate various forms of waste, ultimately achieving higher levels of performance and competitiveness in today’s dynamic business environment.
Frequently Asked Questions
An example of process improvement in Lean is implementing “5S” methodology, which focuses on organizing and maintaining a clean, efficient workplace through five steps: Sort, Set in order, Shine, Standardize, and Sustain.
Value: Identify what adds value from the customer’s perspective.
Value Stream: Map and analyze the entire value stream to eliminate waste.
Flow: Ensure smooth, continuous flow of work or processes.
Pull: Use customer demand to trigger production or service activities.
Perfection: Strive for continuous improvement and excellence in all aspects of the process.
Specify Value: Clearly define and understand what the customer values in a product or service.
Identify the Value Stream: Map out the entire process or value stream, from start to finish, to identify areas of waste and improvement opportunities.
Flow: Create a continuous flow of work, eliminating bottlenecks and interruptions in the process.
Pull: Align production or service delivery with customer demand to avoid overproduction and excess inventory.
Strive for Perfection: Continuously seek to improve processes and eliminate waste to achieve higher levels of efficiency and quality.
Identifying Value: Understanding what the customer values in a product or service.
Mapping the Value Stream: Analyzing the entire process to identify steps that add value and those that don’t (waste).
Creating Flow: Establishing a smooth, continuous flow of work by reducing interruptions and delays.
Implementing Pull: Aligning production or service delivery with customer demand to avoid overproduction.
Pursuing Perfection: Continuously seeking ways to improve processes and eliminate waste, striving for excellence.
The Lean method aims to enhance efficiency, quality, and customer satisfaction while reducing costs and lead times.
Identify Value: Determine what the customer values in a product or service.
Map the Value Stream: Analyze the entire process to identify areas of waste and improvement opportunities.
Create Flow: Establish a smooth, continuous flow of work to reduce interruptions and delays.
Implement Pull: Align production or service delivery with customer demand to prevent overproduction.
Strive for Perfection: Continuously seek improvements, eliminating waste, and aiming for excellence in processes.
The term “Lean” in the context of process improvement does not stand for any specific acronym. Instead, it represents a set of principles and practices aimed at eliminating waste, improving efficiency, and delivering value to customers.
The Lean process plan involves assessing current processes, setting clear objectives, forming teams, training employees, mapping value streams, implementing Lean tools, standardizing procedures, using visual management, measuring performance, encouraging problem-solving, sustaining improvements, and regularly reviewing and adapting the plan.
In Lean, there are typically five levels of maturity or progression an organization can go through:
Level 1: Initial Awareness: The organization becomes aware of Lean principles and concepts but has not yet implemented them.
Level 2: Limited Implementation: Lean practices are introduced in isolated areas or departments.
Level 3: Broad Implementation: Lean is applied more comprehensively across various processes and functions within the organization.
Level 4: Lean Excellence: The organization achieves a high level of proficiency in Lean, with continuous improvement ingrained in its culture.
Level 5: Enterprise-Wide Lean: Lean principles are fully integrated into the organization’s DNA, spanning across all functions and levels, and driving overall business strategy.
These levels represent a progression toward greater Lean maturity and effectiveness in achieving process improvement and waste reduction.
Six Sigma is a data-driven methodology for process improvement that aims to reduce defects and errors to a very low level (3.4 defects per million opportunities). It follows a structured approach called DMAIC (Define, Measure, Analyze, Improve, Control) for existing processes and DMADV (Define, Measure, Analyze, Design, Verify) for new processes or products, using statistical tools and techniques to achieve high-quality results.
Lean process improvement is a methodology focused on optimizing processes by eliminating waste and increasing efficiency. It aims to deliver greater value to customers while reducing costs and lead times. Key principles of Lean include identifying value from the customer’s perspective, mapping the value stream to eliminate waste, creating a continuous flow of work, using customer demand to drive production (pull), and pursuing ongoing perfection through continuous improvement. Lean is widely applied across industries to streamline operations and improve overall performance.
About the Author
