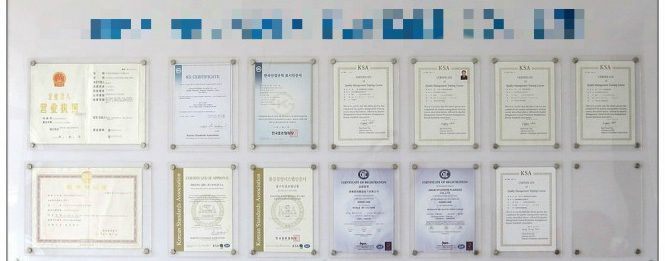
Is your ISO 9001 certification just for the wall?

80-90% of all organisations with ISO 9001 certification has only been certified because of regulatory and/or customer pressure. In such organisations, the management system is often only on the agenda when an audit is coming up. At that time a few people scramble to update dated documents to reflect reality. Will the coming ISO 9001:2015 change this?
This problem is the elephant in the room for many certification bodies and quality professionals. I can’t point to scientific studies that give an exact share of “paper on the wall” certified companies but I have talked with auditors and consultants behind more than 2,000 Danish certifications. They give me this estimate and it has serious consequences. When organisations are certified because they have to, then management often rarely takes real ownership. Instead, they talk about ISO certification 9001 as something that costs money and complicates the business – instead of the other way around.
Who takes this problem seriously?
So why aren’t the many professionals behind ISO 9001 acting on this? I choose to think they are. The draft ISO 9001:2015 standard is the result of a huge effort by thousands of experienced people. A lot of practitioners have already read and interpreted this. Here is my (wishful) interpretation. Besides the changes in terminology and structure, I read the draft ISO 9001:2015 standard as emphasising the following:
The importance of a process approach
Organisations with ISO 9001 certification 2015 need to evolve from focusing on documents to focusing on activities and the processes that can turn them into cross-functional teamwork. A single page value chain diagram will no longer be enough. The result can be fewer words and more action.
The context of the organisation
Quality management principles have to be applied in practice throughout the organisation. This means that the management system has to adapt and change to reflect the daily, collective learning of the people in the organisation – less than the other way around. No more…
“don’t put it into the quality system, then it will be audited and we’ll have trouble changing it!”
as I overheard a manager from a large medical systems manufacturer say recently.
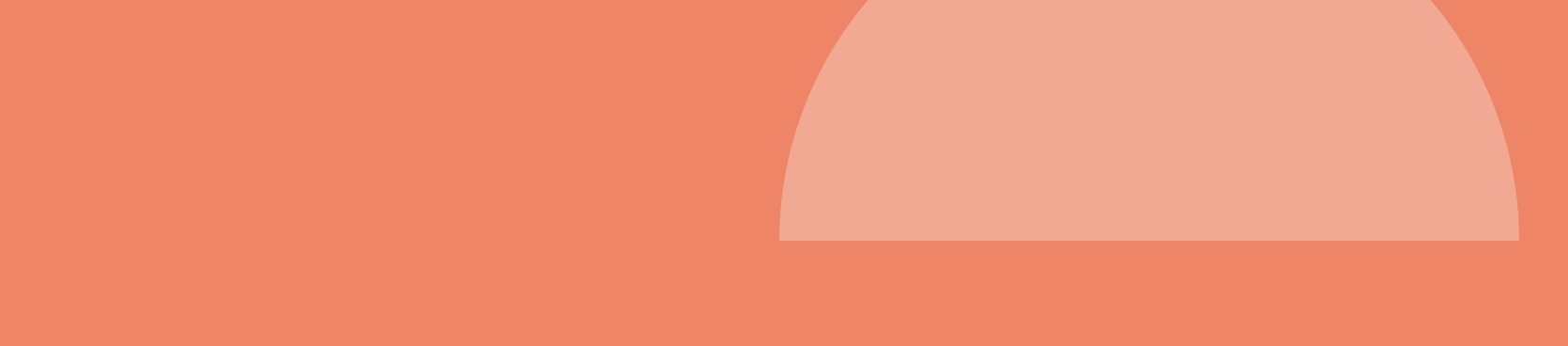
Try Gluu for free
Sign up for a 30-day trial.
No credit card required.
A shift from management to leadership
ISO 9001:2008 uses the phrase “management responsibility”. This can be covered by giving the Quality Manager the responsibility to manage the quality system and the KPI of ensuring successful audits. This is not exactly in line with ISO’s principles for quality management. “Leadership”, on the other hand, will be about executives setting examples with clear, transparent processes, policies and work instructions that they are the first to follow. Management will follow up because if the processes don’t work then the company doesn’t work. (I know what you’re thinking – yes, this will be hard).
The new ISO 9001 certification 2015 and its shift from “Product realisation” to “Operations.”
When a manufacturing company produces a pump then it has to ensure compliance with safety and environmental standards. This is product realisation. When the same company then starts to sell the pump as part of a service to ensure that milk flows through the different processes in a dairy then it gets much more complex. This makes product delivery a number of complex processes and touch points that are managed by many departments. This is complex “Operations” and it requires processes and leadership to get there.
Introducing “Risk-Based Thinking”
I read a good post on how risk-based thinking is natural to all of us so including it in the standard is unnecessary. This may be a point on an individual level but what happens when my risk reduction effort increases your risk? E.g. I’m being extra careful with something and the consequence is that the overall project is delayed and the company loses the contract. This is a systemic risk and it requires a comprehensive process overview of the people involved. People need to understand how their actions affect the overall process. In this light risk-based thinking may be very wise.
Skip the Quality Manual
A quality manual is no longer required (think that was also the case with 2008 though). Instead of creating “documents” organisations need to ensure “documentation“. In practice, this can mean that instead of someone logging everything a system does this for him. E.g. people’s natural dialogue and actions are captured in an activity stream (like we know from Facebook or LinkedIn) that produces the log that we need. Finally, Quality Management can enter the new millennium.
Will ISO 9001:2015 make a difference?
The cynics out there say that the ISO 9001:2008 revision had similar intentions and in reality not much happened. To them I will say that we have a lot to gain if we interpret ISO 9001:2015 as a genuine desire to bring quality management from a perception of “bureaucratic documents telling us how to work” to “our shared understanding of how we work.”
What’s stopping us? The hard part is that this brings the typical quality management professional out of his or her comfort zone. It’s about helping your colleagues to transition to new behaviours by pulling (at least) two levers: Ease of use and involvement.
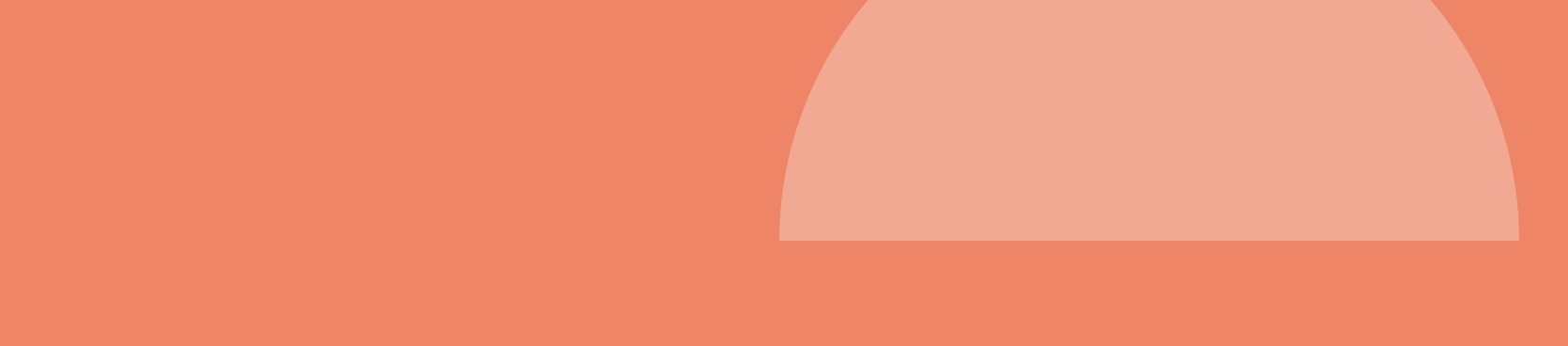
Try Gluu for free
Sign up for a 30-day trial.
No credit card required.
Making it easier to work the right way than the wrong way
Management systems are often designed around the ISO tables of content. Not around the people that use them. Only a few people read through long documents to try to find something that may guide their work. It’s like the manual to your TV. Instead, you get on with your work and only look for information if you have questions or encounter problems. The (quality) management system, therefore, has to make it easier to work the way that the organisation has agreed is current best practice. It’s about reconciling what people say and what people do. No more tedious, manual change control, for instance. No more reporting of non-conformities that will only add to your individual workload.
Getting ownership through involvement of co-workers
Truly involving others is very hard. It requires quality professionals to let go of knowledge. Expert minds bring expert problems (to loosely quote the Lean philosophy). Your way may objectively be the right way but this doesn’t help if your co-workers don’t accept it as their way. Or if they can’t execute it. Confucius sums this up very well:
“Tell me and I’ll forget; show me and I may remember; involve me and I will understand.” – Confucius
So, back to my original question: Will ISO 9001 certification 2015 change anything? I think the answer is “yes” for the organisations where leaders choose to embrace this as an opportunity to get everyone on board. Here are a couple of questions to help you start:
- Are processes inside our (quality) management system easier to execute than similar processes on the outside?
- How many of the processes in our QMS are designed by the people that work with them?
- Would my colleagues agree with my answers?
Now share this classic video with your organisation’s senior manager (don’t tell him to dance – just listen to the narrative):
To get started, you can also use a quality management tool to help involve your colleagues and get everyone on board.
Looking for more? Check out our useful ISO 9001:2015 resources and links.
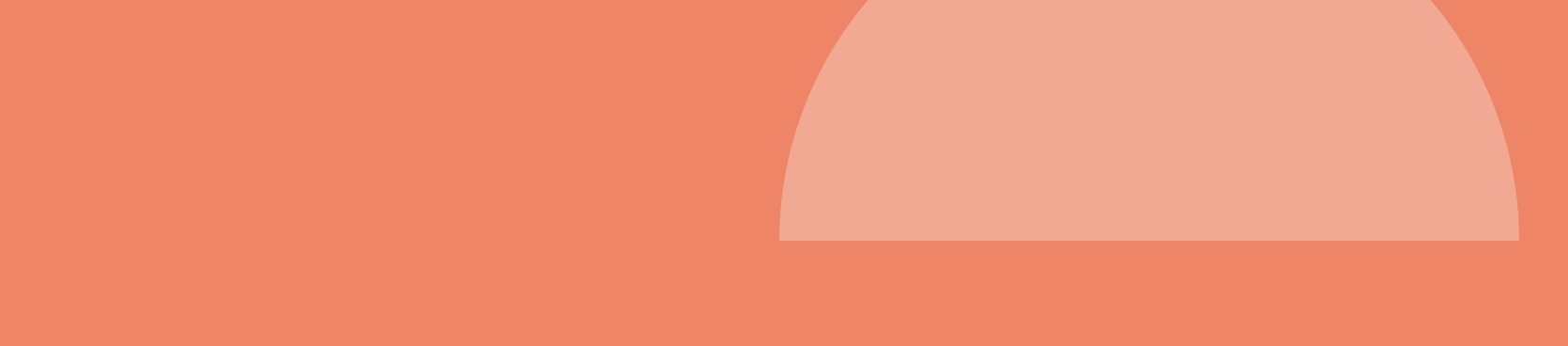
Try Gluu for free
Sign up for a 30-day trial.
No credit card required.
Frequently Asked Questions
The process-based implementation of ISO9001:2015 enables organizations to view their operations as an interconnected network, which promotes efficiency and problem detection and resolution.
When ISO9001:2015 is merely seen as a plaque on the wall, organizations may face non-conformities like poor quality control and low customer satisfaction. The real power of this standard lies in its consistent, comprehensive application.
Digital tools like Business Process Management software can be instrumental in integrating ISO9001:2015 into everyday operations. These tools offer visualization and real-time monitoring of workflows, aiding communication, comprehension, and process control.
About the Author
